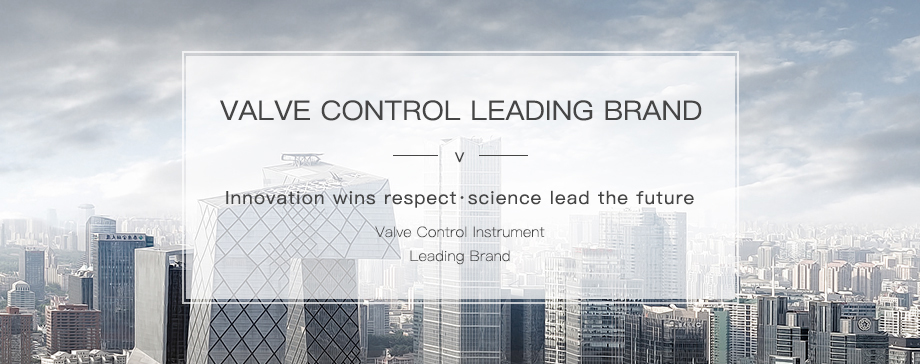
OverviewCategories USE PerformanceStructural features
HCD series electric actuators are manufactured and absorbed by the company using Bernard's technology. HCD series electric actuators are terminal control devices of industrial process measurement and control systems. They can convert system control signals (analog signals or intermittent signals) into mechanical displacements (angle displacement, multi-angle displacement, or linear displacement) and output simultaneously. Torque or thrust, to control the opening of the valve or to control other adjustment agencies, so that the controlled medium work according to the system state.
Rotary actuators are used to drive 90° angle valves, such as butterfly valves, ball valves, dampers, plug valves, and flapper valves.
HCD series electric actuators are safe and reliable, have many types and specifications, high precision, complete functions, light weight, easy installation, debugging, operation and maintenance. They have an international level in the 1990s and have been widely used in energy, metallurgy, petroleum, light industry and chemical engineering. , building materials and other industries play an important role in industrial process inspection and control systems.
The HCD series integral type proportional rotary actuators are divided into two types: Directly connected actuators are directly connected to the valve and other adjusting mechanisms through the output flanges. The pedestal-type actuator is mounted on a basic base and is connected to an adjustment mechanism such as an output arm and a lever and a valve.
Integral proportional adjustment type - that is, the actuator is assembled with the positioning module GAMX in the field.
3、Product use and use environment
3.1 Usage: HCD series electric actuator is a terminal control device in the automatic adjustment system. It receives 4 to 20mA (or 1 to 5V) analog signal and intermittent contact control signal from the regulator or computer, and outputs torque or force. The adjustment mechanism is automatically operated to complete the adjustment task. It can also be used to achieve "manual-automatic" conversion through the electric operator. When switching to manual, the actuator can be used to remotely control the actuator.
3.2 Power Supply Voltage:
Single phase 220V±10%~50HZ
Three-phase 380V±10% to 50HZ
3.3 Ambient temperature and humidity
Temperature: Integral -10~+55°C
Discrete -20 to +70°C
3.4 Relative humidity: not more than 85%
3.5 Media: Non-corrosive media around the actuator.
4、The main technical performance and parameters
4.1 Input Signal: 4~20 mA DC
4.2 Input Channels: Monolithic: 1 Channel, Discrete: 3 Channels
4.3 Input resistance: 250Ω
4.4 Basic error: no more than ±2.5% of rated travel
4.5 Backlash: ±1.5% of rated travel
4.6 Time error of rated travel: ±20% of rated travel time
4.7 dead zone: 3%
4.8 Damping characteristics: no swing, two half cycles
4.9 Insulation resistance: The insulation resistance between the input and output terminals to the ground shall not be less than 20MΩ at an ambient temperature of 10 to 35°C and a relative humidity of less than 85%. The insulation resistance between the power terminals and the input terminals shall not be less than 50 MΩ. .
4.10 degree of protection: in accordance with IEC145 IP65 (required requirements, except for discrete GAMX for indoor installations)
4.11 Work system: intermittent work system with a continuous rate of 50%.
Note: The above technical performance mainly refers to proportional adjustment type electric actuators, which are not involved in remote control type and switch type 1, 2, 3, 4, 5, and 6.
5、Structural features and working principle
5.1 Structural features of the implementing agency:
The actuator is mainly composed of a motor (single-phase or three-phase), a speed reducer, a switch control box, a mechanical limit device, and a hand wheel.
5.1.1 The motor is the power unit of the actuator. The motor has good servo characteristics, ie a high starting torque, a low starting current and a small moment of inertia. A temperature switch is provided inside the stator of the motor for overheat protection. When the motor is abnormally overheated, the switch is opened and the circuit of the motor is disconnected, thereby protecting the motor and the actuator from being burned. When the motor cools down, the switch resumes turning on and the motor resumes operation.
5.1.2 The reducer is generally composed of three stages of deceleration (usually only two stages for multiple revolutions). The first and second stage adopt a planetary gear drive with small volume, large transmission ratio and high efficiency. The second stage of some speed reducers is helical gear transmission. The last stage uses a worm gear, worm or screw nut drive with a large reduction ratio and self-locking performance.
5.2 The speed reducer of a quarter-turn actuator with a speed of not more than 600 Nm is a two-stage planetary gear transmission with a worm gear at the output stage. The high-speed gearbox of the multi-turn actuator is planetary gear transmission and the output stage is helical gear transmission.
5.3 The retarder of not less than 1000Nm rotary actuator is composed of multi-turn actuator reducer with worm gear and worm reducer.
5.4 The switch control box is a standard unit. It consists of a torque limiting mechanism, a stroke control mechanism, an angle sensor, and a terminal block.