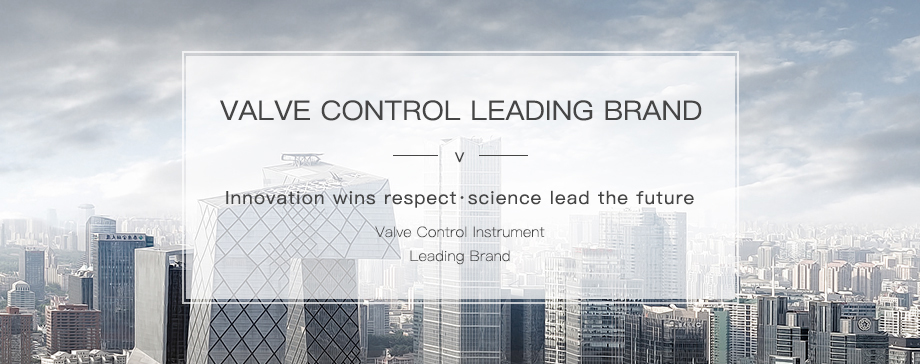
1. Main features of remote intelligent electric device:
1-1* use large scale digital integrated chip, powerful function and high precision.
1-2* electromechanical integration design, small volume and light weight.
1-3* the torque value of the output shaft is measured by the professional current hysteresis sensor, so the accuracy of the torque measurement value is improved. The error rate is less than 5% and can be dynamically monitored and displayed. Overtorque, blocking turn alarm.
1-4* the displacement measurement adopts the optical electromagnetic technology integrated encoder, so the basic error of valve positioning progress is 1.
2. The function of remote intelligent electric device.
2-1* limit protection function.
2-2* moment limit protection function.
2-3* Dynamic indicator contact function
The power device is turning on.
The electric device is running.
Open valve interlock 10. First round operation 11.
Closing moment of the valve.
* valve alarm function 1. Overtorque alarm function a.
3. Turn the alarm function a. Turn off the direction and turn the direction.
* control alarm function
1. Motor overheating protection
2. Control box overheating protection
3. Low battery protection.
4. Internal power failure protection
5. Internal system failure protection
6. Current valve position signal loss protection.
7. Local wiring failure alarm
Ⅱ、HCQ series product technical parameters
model | Output torque (N.m) | Output speed (r/min) | Motor Power (kW) | Rated current (A) | Rated thrust (KN) | Light/dark rod diameter (mm) | Flange number | weight (Kg) |
HCQ10 | 34 | 18 | 0.12 | 1.0 | 44 | 32/26 | F10 | 27 |
24 | ||||||||
36 | ||||||||
48 | ||||||||
HCQ12 | 81 | 18 | 0.25 | 1.3 | F10 | |||
24 | ||||||||
36 | ||||||||
68 | 48 | |||||||
HCQ18 | 136 | 18 | 0.37 | 1.6 | F10 | |||
108 | 24 | |||||||
72 | 36 | |||||||
54 | 48 | |||||||
HCQ20 | 203 | 18 | 0.55 | 2.5 | 100 | 38/32 | F14 | 46 |
24 | ||||||||
36 | ||||||||
48 | ||||||||
HCQ25 | 400 | 18 | 1.1 | 3.4 | F14 | |||
24 | ||||||||
298 | 36 | |||||||
244 | 48 | |||||||
HCQ35 | 610 | 18 | 1.5 | 4.5 | 150 | 54/45 | F16 | 69 |
24 | ||||||||
542 | 36 | |||||||
474 | 48 | |||||||
HCQ40 | 1020 | 18 | 2.2 | 6.5 | 220 | 64/51 | F25 | 190 |
24 | ||||||||
845 | 36 | |||||||
680 | 48 | |||||||
HCQ70 | 1490 | 18 | 3 | 9 | 220 | 70/57 | F25 | |
24 | ||||||||
1290 | 36 | |||||||
1020 | 48 | |||||||
HCQ90 | 2030 | 18 | 5.5 | 14 | 334 | 70/57 | F25 OR F30 | 200 |
24 | ||||||||
1700 | 36 | |||||||
1355 | 48 | |||||||
HCQ95 | 3000 | 24 | 7.5 | 19 | 445 | ~ | F30 |
Table 2. Performance data of HCQM series products (number of adjustments 1200 times/hour)
model | Adjusting torque | Rotating speed(rpm) 50Hz | Flange number | ||||
18 | 24 | 36 | 48 | 72 | |||
HCQM10 | Adjusting torque | 17 | 15.6 | 13.6 | ~ | F10 | |
Maximum torque | 34 | 30 | 27 | ~ | |||
HCQM12 | Adjusting torque | 34 | 34 | 30 | 27 | ~ | |
Maximum torque | 61 | 54 | 54 | 48 | ~ | ||
HCQM20 | Adjusting torque | 81 | 81 | 68 | 54 | 47 | F14 |
Maximum torque | 122 | 109 | 81 | 68 | 54 | ||
HCQM25 | Adjusting torque | 152 | 129 | 102 | 102 | ||
Maximum torque | 204 | 163 | 136 | 136 | |||
HCQM35 | Adjusting torque | 271 | 253 | 203 | 203 | F16 | |
Maximum torque | 544 | 408 | 313 | 218 |
Table 3. HCQL Series Product Performance Data (straight stroke)
model | Flange number | Maximum stem diametermax (mm) | Stroke length (mm) | Actuator output speed (rpm) | 18 | 24 | 36 | 48 | 72 |
HCQL10 | F10 | 26×3 | 115 | Line speed | 0.9 | 1.2 | 1.8 | 2.4 | ~ |
Adjust the thrust | 9.2 | 9.2 | 8.4 | 7.3 | ~ | ||||
Rated push(KN) | 18.43 | 18.43 | 16.26 | 14.63 | ~ | ||||
HCQL12 | F10 | 26×3 | 115 | Line speed | 0.9 | 1.2 | 1.8 | 2.4 | ~ |
Adjust the thrust | 18.43 | 18.43 | 16.26 | 14.63 | ~ | ||||
Rated thrust (KN) | 33.06 | 29.27 | 29.27 | 26.02 | ~ | ||||
HCQL20 | F14 | 32×6 | 115 | Line speed mm/sec | 1.8 | 2.4 | 3.6 | 4.8 | 7.2 |
Adjust the thrust | 31.15 | 31.15 | 26.12 | 20.74 | 18.06 | ||||
Rated push (KN) | 46.87 | 41.87 | 31.15 | 26.12 | 20.74 | ||||
F14 | 38×14 | 115 | Line speed | 4.2 | 5.6 | 8.4 | 11.2 | 16.8 | |
Adjust the thrust | 18.91 | 18.91 | 15.88 | 12.61 | 10.97 | ||||
Rated push | 28.49 | 25.45 | 18.91 | 15.88 | 12.61 | ||||
HCQL25 | F14 | 33×6 | 115 | Line speed mm/sec | 1.8 | 2.4 | 3.6 | 4.8 | 7.2 |
Adjust the thrust | 58.39 | 58.39 | 49.56 | 39.18 | 39.18 | ||||
Rated push | 78.37 | 78.37 | 62.62 | 52.25 | 52.25 | ||||
F14 | 38×14 | 115 | Line speed mm/sec | 4.2 | 5.6 | 8.4 | 11.2 | 16.8 | |
Adjust the thrust (KN) | 35.49 | 35.49 | 30.12 | 23.82 | 23.82 | ||||
Rated push (KN) | 47.64 | 47.64 | 38.06 | 31.76 | 31.76 |
HCQ, HCQM series of multi-turn remote control intelligent electric device driven by the motor, through the worm gear worm deceleration, drive the hollow output shaft rotation. In this gear box, there is a manual/automatic switching mechanism. When the switching handle is in the manual position, the hand wheel is operated, and the hollow output shaft is rotated by the clutch. When electrically operated remote-control intelligent electric device, the manual/automatic switching mechanism automatically falls back, the clutch and the worm gear mesh, the hollow output shaft is driven by the three-phase motor, the torque of the shaft is controlled by the current loop, and the bevel gear meshes on the hollow shaft. Transfer the stroke to the absolute encoder.
The intelligent controller of the multi-turn remote control intelligent electric device receives the standard analog current control signal or the switch quantity control signal and compares with the position signal of the valve position sensor, and the output shaft of the remote control intelligent electric device is positioned corresponding to the input signal. In the position, the positioning control is completed, and the interlocking control, two-wire control, or event signal can be used to position the control system at a preset position unless the output shaft torque value of the remote intelligent electric device is greater than the rated torque during the operation. Value or set the torque value, otherwise the intelligent controller of the remote intelligent electric device will meet the requirements of the control system, issue the correct instruction, trigger the three-phase solid state relay or AC contactor, make the motor turn on the three-phase power, and drive the remote control intelligence The electric device operates normally.
The multi-turn remote control intelligent electric device adopts a non-invasive design, and the parameters and functions of the electric device can be corrected or configured through a handheld remote controller.
HCQL direct-travel remote control intelligent electric device is based on the HCQM multi-turn remote control intelligent electric device, and is additionally composed of a trapezoidal nut screw, a flange bracket and an adjustment stroke mechanism. Convert multi-turn torque and speed into linear motion stroke and exit thrust.
Angular-stroke remote control intelligent electric device is based on HCQ, HCQM multi-turn remote control intelligent electric device, and it is composed of a combination of two-stage worm gear reducer.